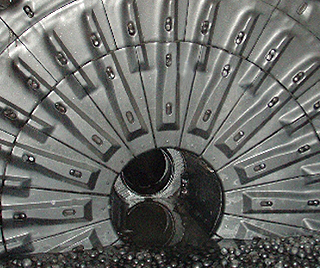
Castings & Liners
Crushing activities involved in mining, quarrying or recycling are carried out by impactors which are either Vertical Shaft Impactors (VSI) or Horizontal Shaft Impactors (HSI).
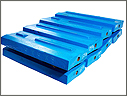
The central piece of Horizontal Shaft Impactors is the rotor. It can be fitted with either four lines of x hammers or with four Blowbars positioned in a star. When turning, the rotors will rotate the hammers or the Blowbars at a certain speed in order to break the rocks fed in through the top. An ideal Blowbar is a fusion of best suited design and alloy. The optimum design to best crush the feed material together with the best alloy resisting against wear and shocks will together maintain the blow bar's original profile constant. Advantages of a Blowbar :
|
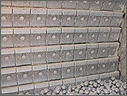
- Increase in crusher efficiency
- Increased quality of production by keeping the initial wear profile constant
- Optimized maintenance with fewer required adjustments of the impact plates
Side Liners
Side Liners are produced in White Iron, Low Chrome and Medium Chrome for application in Gravel Pits and Quarries, in a Horizontal Shaft Impactors unit.
Impeller
A standard Vertical Shaft Impactors unit uses a Rotating Impeller with iron wear shoes and a chamber with Anvils. An ideal Impeller has to maintain an optimum balance between the design and the materials used to achieve best performance, based on the composition of the feed.
Anvils
A standard Vertical Shaft Impactors unit uses a Rotating Impeller with iron wear shoes and a chamber with Anvils. An Anvil type crushing chamber consist of 15 to 20 Chrome iron blocks positioned around the circumference of the machine against which the rotor throws the rock to be crushed.
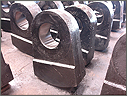
- Reduction in wear costs
- Maintaining optimum crushing performance
- Reduced maintenance of spare parts improves manpower safety